of MGH Consulting Ltd. is the second of a series of
contributed editorial columns. Readers interested in
authoring a future contributed column can click here
to read the Guidelines for Editorial Submissions page.
Responding to the
European Commission's
WEEE & RoHS Directives:
Electronics & appliance manufacturers must consider environmental impact beyond the point-of-sale.
by Justin Voyle
If you are a producer of electric and electronic equipment and if you manufacture, resell or import your own brands in the European Community, August 13, 2004 is a date you should have in your diary.
Why? On this date the first of two important European Commission directives come into force, which just might change the way you think about the design, manufacture, repair, and refurbishment of your products in Europe.
If this doesn�t ring any alarm bells just yet, what about if in the future you also have to consider the environmental impact of your products, well beyond point-of-sale by assisting, and contributing to the cost of disposing and/or recycling goods you sold? Does this interest you? I hope so.
There is little doubt that the aim of the proposed Waste Electrical and Electronic Equipment (WEEE) and Restriction of certain Hazardous Substances in electrical equipment (RoHS) directives are clear -- to minimise the environmental impact of electrical and electronic equipment across Europe. In the United Kingdom, the current environmental impact is significant. Estimates suggest 915,000 tonnes of electrical and electronic equipment (EEE) is discarded each year and forecasts suggests this is rising by between 3% and 8% per year. Household appliances and IT equipment constitute 85% of this waste (see Figure 1).
But don�t worry if this is news to you. Recent research has indicated that nearly 81% of UK companies are unaware of the WEEE directive. Is this a consolation or a worry?
And what about markets beyond Europe? Although WEEE targets have not yet been set in the U.S., the European precedent does prompt careful consideration of how future directives may affect U.S. industries.
WEEE: Encouraging Product Life-Cycle Management
Targeting the EEE waste stream by encouraging product end-of-life management, eco-friendly design, life-cycle thinking, and extended producer responsibility in Europe demonstrates a clear and marked shift towards a combination of regulatory, financial and voluntary mechanisms. But what is not so clear, as of yet, is just how producers will plan and mobilise to implement many of the changes required.
Figure 1
UK WEEE Arisings
(Average 1996 & 1998 Data)
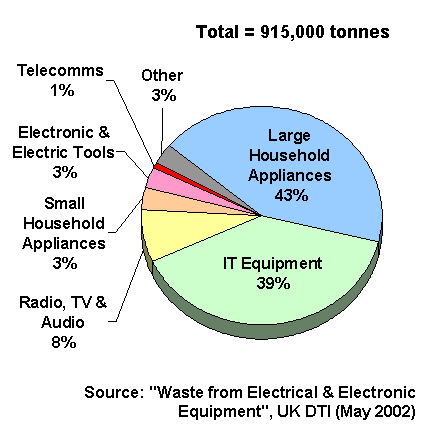
The WEEE directive specifically aims to reduce waste, increase recovery and recycling and improve the environmental performance of producers. Almost every type of electrical product is included in 10 broad categories, ranging from household appliances, IT and telecommunications equipment, to medical equipment, and toys.
As well as encouraging designs that make dismantling and recycling easier (and �appropriate� measures so that producers do not prevent WEEE re-use), WEEE specifies:- Separate collection -- options to be determined and in place by December 2006 to achieve a four-to-six-kilogram per head target;
- Specified treatment -- for the removal of all fluids, certain substances and some components, e.g. batteries, PCB�s <10cm2, CRT�s etc. (currently 70% of WEEE in the UK is disposed of without treatment);
- Recovery and re-cycling targets -- applied to separately collected WEEE, i.e. categories not products (e.g. IT and Consumer -- 80% by weight reclaimed/recovered and 75% by weight recycled/re-used) to be achieved by December 2006 �- this also includes historic pre-directive WEEE; and
- Producers to cover the costs of collection, treatment and disposal -- directive states that by August 2005 producers should provide financing for the collection, treatment, recovery and disposal from private households and accommodate business-to-business WEEE -� for products that enter the market after this date producers only have responsibility for financing disposal of their own products.
Despite WEEE being a complex waste stream that requires several levels of reprocessing and recycling expertise to ensure the maximum value is recovered, the directive raises a number of more fundamental business issues to which, as of yet, little guidance or thought has been given. These include:
- Setting and monitoring recovery & re-cycling targets for each European country and product category;
- Determining collective or individual producer responsibility;
- How to deal with historic waste? Is it fair that it�s shared by all existing producers?
- How to deal with orphan products?
- How to finance the directive without avoiding visible fees for the consumer (estimates suggest the additional costs of dismantling and treating hazardous substances in the UK is £36 million).
There is little doubt there is an opportunity for producers to work together. Forging ahead with a solution in the time frame available does pose some problems, especially if internal change initiatives also have to be dealt with, e.g. to understand the impact on a distributed repair network.
Supply chains have never been so complex. Many products are not designed or engineered to support closed-loop product life-cycle management (design for repairability and sustainability will have to be intrinsic). Also existing enterprise architectures and applications only look forward and give little consideration to returns management etc. WEEE is likely to affect nearly all aspects of the business ecosystem.
RoHS: Removing Hazardous Materials
Complimentary to the WEEE directive is RoHS, which in essence, is a single market directive on the restriction of certain hazardous substances during manufacture. From July 1, 2006, substances such as lead, mercury, cadmium and chromium will be banned. This will obviously have huge ramifications. An obvious example of the effect of this requirement is with the widespread use of lead-based solders on printed circuit boards and the use of lead in cathode ray tubes. Although industry has been arguing there are many cases where solders cannot be substituted in the short-term, there is little doubt substitutes (such as silver-bismuth-copper), which have been in development for more than 10 years, will have to be introduced.
Just as with WEEE, this raises a number of fundamental business issues which need to be addressed by the European Commission and producers, namely:
- How to deal with historic pre-directive manufactured components � should they be replaced during repair and refurbishment?
- Accommodating the associated tooling, training and material costs; and
- Adjusting the repair network to handle changes in repair practices.
Immediate Financial Impact
The cost impact to producers of both directives is likely to be significant in the short-term, as producers race to establish the necessary mechanisms to meet recovery, recycling and treatment targets, as well as in the longer term, as alternative manufacturing and repair materials, components and substances are introduced (see Figure 2).
Figure 2
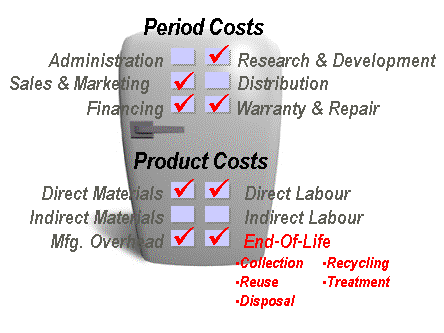
In addition to this, there are also likely to be significant health and safety, tooling, and training implications, which will obviously have an impact on fixed assets and the cost of sales. Consideration might also have to be given to existing levels of inventory, which may have to be run-down or written off. All of these factors will have a cost implication to producers and may ultimately impact their net working capital in the short-to-medium term (see Figure 3).
Figure 3
MGH Consulting's
WEEE & RoHS Operational Review Framework
Focus on a Current State Assessment
The issue should now be: what can and should be done to prepare for the impact of both directives?
Organisations should firstly consider beginning with a current state assessment of the "As-Is" situation, which will scope and size the issues at hand and provide an indication of the depth and breadth of the change agenda. This initial fact finding and data-gathering phase of work could include:
- Existing end-of-life processes review to determine capability to deliver and change readiness and identify opportunities to increase refurbishment, reuse, recycling, pre-treatment, and treatment across the boundaries of the enterprise and into the supply chain;
- Review of WEEE and RoHS directive requirements and how they apply to specific product groups and various geographic markets;
- Industry benchmark analysis to understand delineation of responsibility, quantify likely targets and the extent to which prioritised needs are to be addressed;
- Strategic option development to identify a number of options (positioning alternatives) for the "To-Be," including key business processes, operating principles, and associated transition or implementation issues; and
- Business case development to quantify the costs associated with the necessary change across various options.
At the end of a current state assessment, an organisation should have no concern answering the following questions:
- Do we understand WEEE and RoHS and how it applies to our organisation, products and supply chain?
- Do we know what we should do in preparation for August 2004 and July 2006?
- Do we know what we have to resolve to meet our own targets and milestones?
- Do we know what capabilities we have or don�t have to meet our plan?
- Are we comfortable we can keep it going?
Moving towards Implementation
What should follow a current state assessment is a sequence of further activities (see Figure 4) and phases of work aimed at further refinement of:
- strategic options,
- further quantification of costs,
- implementation planning, and
- roll-out.
Figure 4
Industry Pressures Driving Warranty & End-of-Life Costs
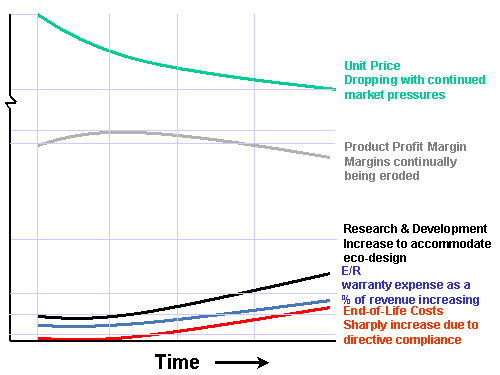
Act Now
It is worthwhile noting that it is not only electrical and electronic equipment producers that are under pressure to improve their use of resources and reduce the amount of waste. Back in 1997, the European Commission proposed a directive on the disposal of end-of-life vehicles despite the fact that -- with an average recycling rate of 75% -- the automobile is one of the most recycled complex products in the EU. However, the Commission faced industry opposition, and it took three years before the End-of-Life Vehicles directive 2000/53/EC was passed. It requires:
- The original vehicle manufacturer to be responsible for taking back the vehicle at the end of its life.
- Disposal to landfill of certain specific hazardous substances (e.g. heavy metals) were to be reduced virtually to zero.
- Targets (by weight fraction) were set for increased levels of material recovery, and most recovered material had to be either re-used or recycled, with only a small fraction being permitted to be reprocessed for energy recovery. The specific targets are:
- By 1 Jan. 2006: 85% to be recovered (minimum 80% recycling)
By 1 Jan. 2015: 95% to be recovered (minimum 85% recycling)
There is little doubt that if organisations have yet to consider the potential impact of the WEEE, RoHS, and ELV directives, then there is much to do. The good news, however, is that a great deal can be achieved in a relatively short period of time, but there can be no complacency. Only if the impending change is taken seriously can organisations plan and mobilise in a cost effective manner. But don�t think this is a flash in the pan and a one-off threat to the way you do business. Other pending regulations such as those relating to Special Waste, Ozone Depleting Substances, Batteries, and Landfill may also impact on the way you do business.
